Spinning forming process
- Metal Spinning Process - YouTube.
- What is Wet Spinning | Principle and Uses of Wet Spinning - Textile Learner.
- Flexible Spinning Forming Technology.
- Understanding Metal Spinning: Conventional vs. Shear Forming.
- Spinning Process - an overview | ScienceDirect Topics.
- Melt Spinning Process: Manufacturing, Advantages and Disadvantages.
- CN102814621A - Automobile hub isothermal forging and spinning forming.
- Metal Spinning Versus Flow Forming.
- Manufacturing Process Meaning amp; Types Casting, Froming.
- Roll Forming: What is it? Process, Benefits, Types, Metals Used.
- Tube End Forming Technology | Spinning | Flanging | T-DRILL.
- Flow Forming or Metal Spinning - InTradeFairs.
- Welcome to AW Metal Spinning Company - Brevard, Central Florida.
- Tube Bending, Forming Process, Custom Metal Fabrication - Bohn amp; Dawson.
Metal Spinning Process - YouTube.
Steps in Spinning Process. Step 1Metal Forming. This step involves the laying down of the material onto the mandrel. It is accomplished with short inside to outside moves.Material gets easier to form as the part is closer to completion. Steps In Sheet Metal Forming Process. Step 2Trimming. Parts having been spun are trimmed at the end to. In the GROB spinning process, discs are formed into cup-shaped blanks, whereby spinning wheels forms the material over a spinning mandrel. BENEFITS... All machine parameters relevant to the forming process can be set and changed via the CNC controls of the machine, providing rapid and flexible response to material-specific variations e.g. The procedure of spinning involves the extrusion of an appropriate liquid solution through the spinneret in a chemical bath that coagulates the solution into filament strands. These filament strands are then drawn out of the bath, washed and dried before being wound on the spools.
What is Wet Spinning | Principle and Uses of Wet Spinning - Textile Learner.
Hot spinning refers to the process of spinning a piece of metal on a lathe while a high beam of heat is directed to the workpiece. After the workpiece is heated, the subject metal is then shaped whereby the lathe is pressed against the heated surface. Necking or reduction of the diameter can still be achieved through the hot spinning technique. Jul 21, 2022 Here we collect three unique bursts, GRBs#92;#92;,060614, 211211A and 211227A, all characterized by a long-duration main emission ME phase and a rebrightening extended emission EE phase, to study their observed properties and the potential origin as neutron star-black hole NSBH mergers. NS-first-born BH-first-born NSBH mergers tend to contain fast-spinning non-spinning BHs that more easily. Flowforming enables the one-piece construction of assemblies and saves money in material, inventory, tooling, and assembly. This metal forming process enables PMF to manufacture finished parts using less material, and therefore, it is cost-effective. One piece construction also eliminates the need for non-destructive testing which is typical in.
Flexible Spinning Forming Technology.
Spin forming is unlike other metal forming processes that cut and remove material to produce the desired shape. The right metal spinning equipment and metal spinning tools transform a metal disc or tube into a quality spun finished piece.... The metal spinning process can be performed either hot or cold, depending on the piece of metal being. Metal Spinning Technology. June 25, 2019. This article, the first of a series on metal spinning processes and tools, provides an overview of the technology. Metal spinning is a near-net-shape forming process used to produce axisymmetric hollow parts, usually with circular cross-sections, that involves forming sheet metal over a rotating mandrel. STEPS IN SPINNING PROCESS Step 1 Metal Forming This step involves the laying down of the material onto the mandrel. It is accomplished with short inside to outside moves. Material gets easier to form as the part is closer to completion Step 2 Trimming Parts having been spun are trimmed at the end to blunt sharp edges and also to.
Understanding Metal Spinning: Conventional vs. Shear Forming.
Our six primary metal forming and fabrication processes are all supported by secondary processes to build parts to customer specifications. Specializing in stainless steel work, our highly knowledgeable craftsmen can work with a variety of metals in all applications.
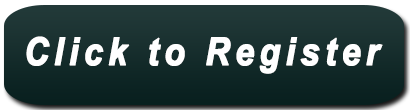
Spinning Process - an overview | ScienceDirect Topics.
Shear spinning is a process related to conventional spinning and is also known as flow turning or spin forging. In a conventional spinning operation the work is essentially formed by bending. There is usually not much change in the thickness of the sheet metal.
Melt Spinning Process: Manufacturing, Advantages and Disadvantages.
Flow forming which we refer to as quot;Floturningquot; differs essentially from metal spinning in that the metal is coldflowed, using tremendous pressure on the forming roller. In addition to controlling section thickness, Floturning improves metal structure in the coldworking process. The Floturning process is an outstanding example of quot;net-to. 37. _____ forming process is also called as Tube Spinning. aSheet metal Spinning bShear Spinning cFlow dcircular Ans:- c 38.The ______________ process involves applying compression to the outside diameter of cylindrical perform by combination of axial an radial forces using a set three or four rollers. aSheet metal Spinning bShear. Sheet metal forming process is done on a press and the parts are formed in between two die. The die at the top is called a punch.... Spinning. The sheet metal is revolved at high speed and is pressed against a prior attached headstock spindle. A tailstock supports the metal while it is spinning. With a special tool, pressure is applied to the.
CN102814621A - Automobile hub isothermal forging and spinning forming.
Advantages Of Stretch Forming Stretch forming has the following advantages over conventional press forming methods: Approximately 70 less force is needed than that required for conventional press forming. Stretch forming can reduce material costs by as much as 15. Although allowance must be made on the stock for gripping, it is gripped on.
Metal Spinning Versus Flow Forming.
Spinning is a sheet metal forming process in which a metal blank is pressed over a rotating chuck or form mandrel with the help pressing tool to obtain axisymmetric hollow shell. The sheet metal parts that have circular cross-section can be made by this process. Dry Spinning: In dry spinning, the fiber-forming polymer dissolved in a volatile solvent is introduced into a heated drying chamber where the solvent is evaporated and solid fiber is obtained through a spinneret. Dry spinning is suitable for producing fire denier fibers. It also no need for washing. A flowchart of the dry spinning process is. Wet spinning is a fiber-forming process in which the polymer is dissolved in a solvent and the solution is extruded into a chemical bath. It is a traditional technique to develop polymer-based fibers. The wet spinning method was first used in the manufacture of rayon Chardonnet Silk by extruding the alcoholic solution of the cellulose nitrate.
Manufacturing Process Meaning amp; Types Casting, Froming.
The spinning process and its mechanism have been studied by number of researchers. The natural silk synthesized by the silkworm and spun in the form of a silk cocoon is synthesized in the silk gland. The silk gland of B. mori is a typical exocrine gland secreting a large amount of silk proteins. Metal spinning is a method of forming rotationally symmetrical sheet metal parts. In spinning, the sheet metal discs are formed into rotationally symmetrical hollow shapes.... If a product is being spun by one of our skilled hand spinners, the same process is used but the operative applies the metal spinning roller by hand. Superplastic forming is a process dedicated for sheet material allowing elongation of several hundred percent. We use SPF to form titanium, nickel or Aluminum alloy parts at high temperature with either gas or die pressure. SPF allows the forming of very complex shapes. Contact us about this product. Hot Forming amp; Superplastic Forming Machines.
Roll Forming: What is it? Process, Benefits, Types, Metals Used.
The metalworking process known as quot;metal spinningquot; goes by many different names, such as spin forming, metal forming, metal turning, CNC metal spinning, or just quot;spinning.quot; Metal spinning is a process whereby a sheet of metal, cut into a flat metal disc, or blank, is formed into different symmetrical rounded shapes through spinning it. The typical spinning process heats the preform to provide the required ductility and often distorts the final part during cooling. Flow forming is a cold forming process, which ensures the final part#x27;s controlled characteristics are to design with no distortion. Metal spinning and flow forming are similar processes. Whether the blank is flat or a preformed metal sheet, it#x27;s important to understand the differences between conventional metal spinning and shear forming. So, let#x27;s go over the basics: #1. Conventional Metal Spinning. Rollers push the material over the mandrel#x27;s contour, leaving the material thickness at a constant throughout the process.
Tube End Forming Technology | Spinning | Flanging | T-DRILL.
SPINNING is a method of forming sheet metal into seamless, axisymmetric shapes by a combination of rotation and force. Based on techniques used, applications, and results obtainable, the method can be divided into three categories: Manual spinning, Power spinning, Tube Spinning. Metal spinning, as a kind of rotary forming process, is widely applied in the production of various areas. In this paper, the mathematical model of the conchoid roller path is proposed based on.
Flow Forming or Metal Spinning - InTradeFairs.
Bending of sheet metal is a common and vital process in manufacturing industry. Sheet metal bending is the plastic deformation of the work over an axis, creating a change in the part#39;s geometry. Similar to other metal forming processes, bending changes the shape of the work piece, while the volume of material will remain the same.
Welcome to AW Metal Spinning Company - Brevard, Central Florida.
Process The spinning process is fairly simple. A formed block is mounted in the drive section of a lathe. A pre-sized metal disk is then clamped against the block by a pressure pad, which is attached to the tailstock. The block and workpiece are then rotated together at high speeds. T-DRILL is the globally leading provider of tube and pipe fabrication solutions. For more than three decades, T-DRILL kept developing solutions for diverse applications in many industries, resulting in countless success stories in more than seventy countries.
Tube Bending, Forming Process, Custom Metal Fabrication - Bohn amp; Dawson.
The spinning process frequently requires a series of passes to complete the formed part. As each pass is made the metal is stretched, thinning out the material as a result. Thinning out is typical of the conventional spinning process but it can be minimized when required. Shear Spinning. This process is majorly used in the manufacturing of kitchen utensils. Hot Spinning: Hot spinning is the process of metal forming where the metal blank is heated to forging temperature and then converted to the desired shape. The metal is forced to flow over a rotating shape by the pressure of the blunt tool.
Other links:
Christchurch Casino Email Address
World Series Of Poker Highlights